Silverson Homogenizer Mixers
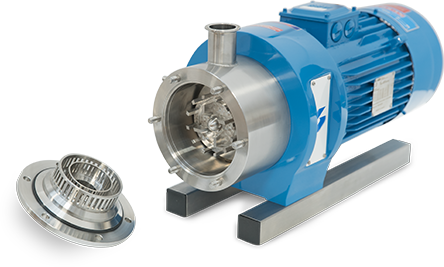
Silverson Homogenizer Mixers
Silverson Homogenizer Mixers deliver rapid, uniform homogenization with droplet and particle sizes typically in the 2–5 micron range, ideal for a wide variety of products including creams, lotions, ointments, sauces, and flavor emulsions. In many cases, even finer results down to 0.5 microns can be achieved, depending on the formulation and ingredient profile.
We offer in-tank, in-line, and lab-scale benchtop homogenizers, each utilizing our precision-engineered rotor/stator workheads.
Efficient, Uniform Homogenization
Unlike high-pressure homogenizers, which are often complicated to operate, costly to run, prone to clogging, and require frequent maintenance, Silverson systems use a precision-machined rotor/stator design engineered for simplicity, reliability, and efficient performance. This approach delivers the intense shear required to produce stable, homogeneous products—without the operational drawbacks of high-pressure equipment.
Seamless Scaling from Lab to Production
Silverson offers solutions for every stage of product development. Our L5M-A lab mixer uses the same core technology as our production-scale equipment, allowing formulations developed in R&D to be reliably scaled up to manufacturing volumes. All units are built to the same high engineering tolerances, ensuring consistency from bench to batch and simplifying process validation.
High Shear: A Smarter Alternative to High-Pressure Homogenizers
Compared to high-pressure systems, Silverson high shear homogenizers offer several key advantages:
- Significantly lower capital expenditure
- Reduced energy consumption
- Higher processing capacity
- Simple to operate, maintain, and clean
And when a high-pressure homogenizer is required—such as for submicron applications—a Silverson mixer can serve as a powerful pre-processing step, delivering a finer, more uniform premix that improves throughput and may eliminate the need for multiple passes or additional equipment. Silverson homogenizers can also complement or serve as an alternative to colloid mills, offering a more efficient or flexible solution depending on the application.
We regularly help customers improve their process efficiency by integrating Silverson high shear mixers with existing high-pressure systems. Request a quote or speak with our team →
Powerful, Precise Homogenization
At Any Scale
Ready to explore your options? Browse our mixer range below.
How It Works
Silverson homogenizers deliver fast, efficient, and aeration-free mixing through the application of intense high shear—minimizing processing time and often eliminating the need for auxiliary pumps. Inside the workhead, a three-stage mixing process precisely breaks down particles and droplets to produce stable, uniform emulsions and dispersions. Here’s how it works:
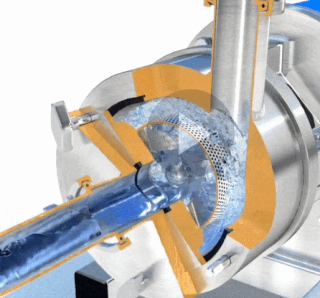
The high-speed rotation of the rotor blades creates a powerful suction that draws liquids and solids into the precision-machined workhead.
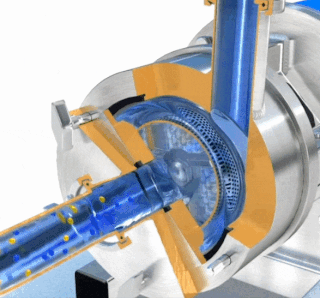
Centrifugal force propels the product outward into the narrow gap between the rotor blades and the inner wall of the stator, where it undergoes a precision milling action. This stage begins the breakdown of particles and droplets to a smaller, more uniform size.
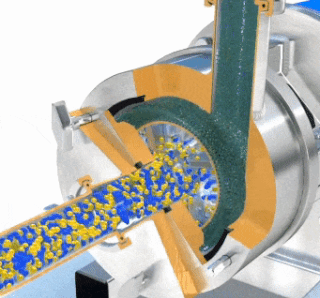
The product is then forced at high velocity through the stator’s perforations, subjecting it to intense mechanical and hydraulic shear. As the mixture exits through the outlet, fresh material is continually drawn into the workhead, progressively reducing globule or particle size, ultimately delivering a completely homogeneous and uniform final mixture.
-
1. Rapid Intake
1. Rapid Intake
The high-speed rotation of the rotor blades creates a powerful suction that draws liquids and solids into the precision-machined workhead.
-
2. Uniform Reduction
2. Uniform Reduction
Centrifugal force propels the product outward into the narrow gap between the rotor blades and the inner wall of the stator, where it undergoes a precision milling action. This stage begins the breakdown of particles and droplets to a smaller, more uniform size.
-
3. Homogeneous Result
3. Homogeneous Result
The product is then forced at high velocity through the stator’s perforations, subjecting it to intense mechanical and hydraulic shear. As the mixture exits through the outlet, fresh material is continually drawn into the workhead, progressively reducing globule or particle size, ultimately delivering a completely homogeneous and uniform final mixture.